A presentation on 3D optical scanning and 3D printing
January 20 2023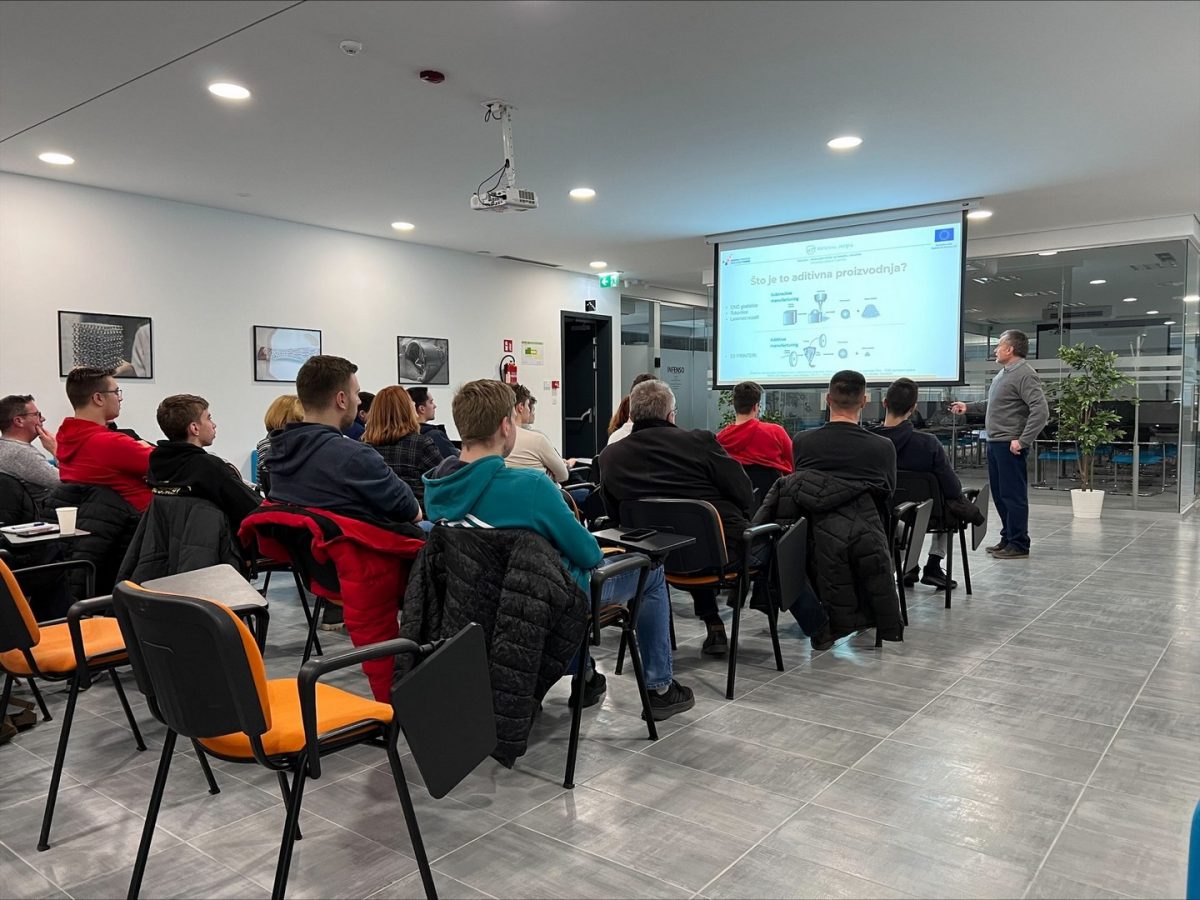
A presentation on 3D optical scanning and 3D printing was held at the initiative of CroFa and our partner Metalska jezgra. Several representatives of foundries (Duni, Werner Metal, Ferro-preis and Ljevaonica Duga Resa) attended, as well as other interested institutions and companies.
The presentation was given by the employees of the Metal Core: Dr. sc. Marina Grabar Branilović, Ph.D. Ivana Mihalic Pokopec and Zoran Kadežabek, inf.
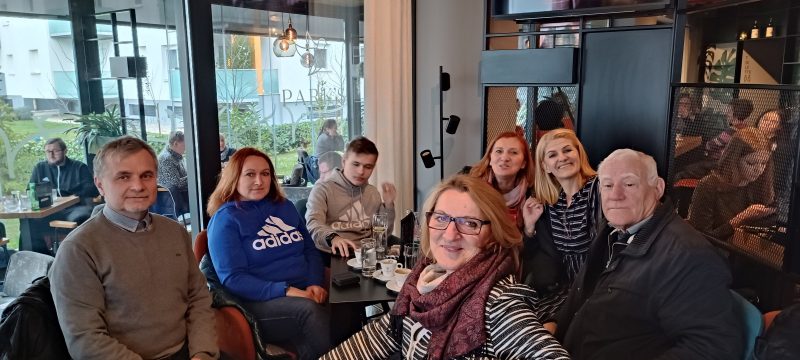
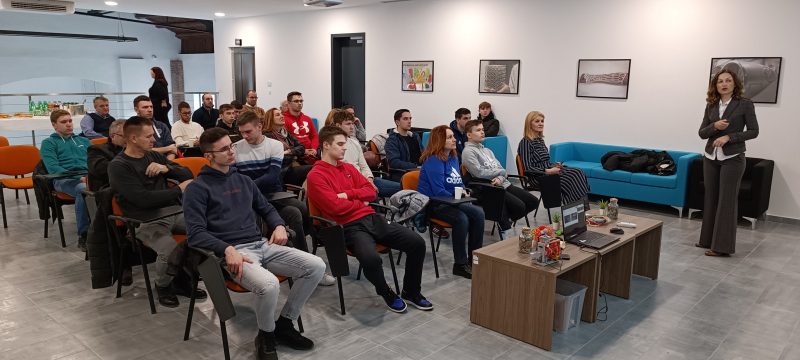
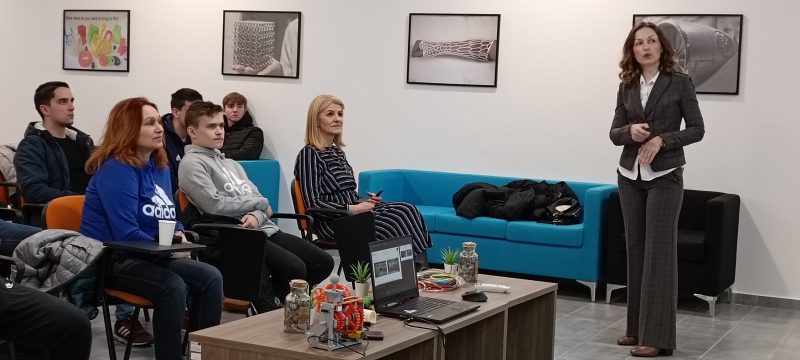
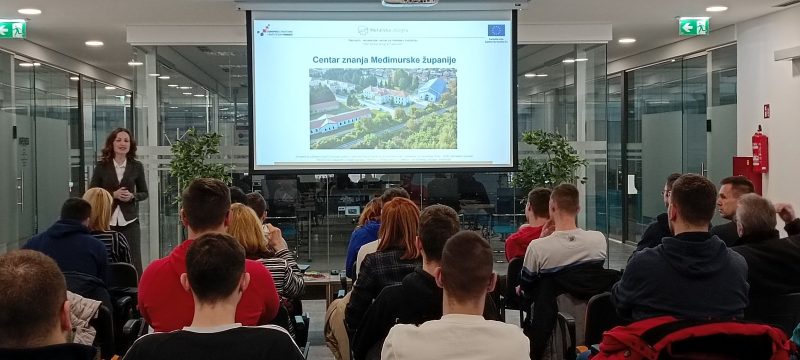
In the introductory part, the head of the Department for Research and Development of the Metal Core Čakovec, Ph.D. Marina Grabar Branilović greeted everyone present in front of the whole team and introduced them to the Institution itself. It was presented to them when and how the Metal core was created, what is its vision and area of activity. She then gave a presentation on 3D optical scanning and the ATOS 5 12M XL scanner. 3D optical scanning is a process by which a real object is mapped into a digital form. The 3D scanning process itself has a very wide range of applications: industrial design, reverse engineering and prototyping, quality control, documentation of cultural artifacts, archiving of archaeological finds, dentistry, film industry, creation of virtual worlds in computer games, etc. A 3D scanner is a device that analyzes space and in doing so, it collects data on the shape and structure of the object it is scanning, and the obtained data is used to create a 3D model. It is about measuring and recording without touching the surface. The metal core has a measuring system for 3D optical measurement ATOS 5 12M XL, all parts of which were developed and manufactured by the company GOM (Zeiss). The given system uses blue light technology (“Blue Light Equalizer”). In addition to the projector with structured blue LED light on the scanner head, there are also two cameras with a resolution of 12 megapixels that detect the light reflected from the object being scanned. Two measuring areas are available in the Metal core: 700 x 500 mm2 and 320 x 240 mm2. Also, there is a photogrammetric upgrade for ATOS for the needs of measuring large objects and 3D measurement of displacements and deformations in discrete points (digital measurement camera with DX format sensor (CMOS color sensor, resolution 21 million pixels, sensor size: 23.5 x 15 .7 mm). ATOS Professional software is used for management, control and analysis. More about ATOS 5 12M XL can be found at: https://www.gom.com/en/products/high-precision-3d-metrology/ atos-5. Examples of performed scans and their results are presented.
This was followed by a lecture on additive manufacturing, which was held by Zoran Kadežabek, inf., employed as a key expert in the Internet of Things Department of Metal Core Čakovec. Additive production is increasingly present in the working branches of activity. The production process begins with the construction of a 3D model using computer CAD modeling programs or by scanning an object with a 3D scanner, on the basis of which we obtain its digitized spatial form. The model is then converted into a series of horizontal cross-sections that are 3D printed layer by layer to the final product. Prototypes, molds and high-precision tools, as well as ready-to-use functional parts, can be made equally successfully with these procedures. The leading system for direct digital production from polymers was presented – Stratasys F900, available in Metalska jezgra. This system uses FDM (Fused Deposition Modeling) technology. The parts are built layer by layer from polymer material that passes in the form of a wire through a nozzle where it heats up and melts. During the production of the product, the material is extruded and placed in the desired places in very fine layers. Its working volume (WxDxH) is: 914.4 mm x 609.6 mm x 914.4 mm. More about the Stratasys F900 3D printer can be found at: https://www.stratasys.com/en/3d-printers/printer-catalog/fdm-printers/f900-printer/. As part of the presentation, examples of 3D printing made in Metalska jezgra Čakovec were presented.
dr. sc. Ivana Mihalic Pokopec, head of the Department of Technology, presented a system for direct digital production from metal using additive technology – EOS M 290, available in Metalska jezgra. This system uses DMLS (Direct Metal Laser Sintering) technology. Its working volume (WxDxH) is: 250 mm x 250 mm x 325 mm. 3D printing of metal parts is done directly from a computer model, and the basic material in the process is metal alloy powder. The working principle of DMLS technology is based on three steps: the applicator distributes the metal powder on the work plate, the laser in each layer melts the metal powder according to the given shape and the printed piece grows layer by layer. The advantages of such technology are that it enables freedom in modeling the desired shapes (it is a perfect solution when classic production technologies reach their limits) and the creation of very complex structures. Then, DMLS technology results in high productivity (production of prototypes at an early stage of development, faster product development, faster market entry) and individual solutions. The given technology is used in the aviation industry, electronics, medicine, in the production of turbines and turbo machines, in toolmaking, the automotive industry, etc. As part of the presentation, various examples from practice realized in the Metal core were presented. More about the EOS M 290 3D printer can be found at: https://www.eos.info/en/additive-manufacturing/3d-printing-metal/eos-metal-systems/eos-m-290.
The presentation was followed by networking with all the visitors socializing, sightseeing and familiarization with the equipment
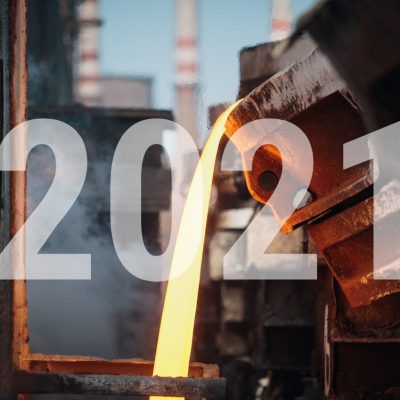
Foundry production in Croatia 2021
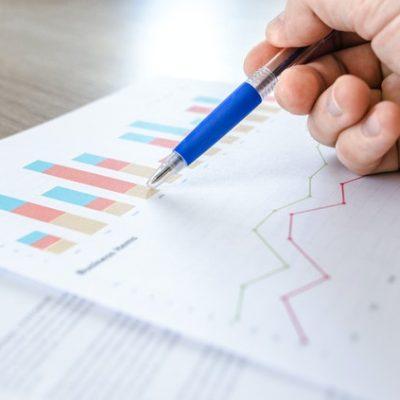
2022 form